Conrad Kacsik can meet a variety of needs with custom-designed systems for monitoring and controlling various process variables, such as temperature, pressure, flow and more.
Our engineering team installs easy-to-use systems and supervisory control software that work with standard PCs, providing simple operation, configuration, programming and access to critical data. These systems and software help providers in a wide array of industries meet demanding tolerances and deliver consistent results. To learn more about how Conrad Kacsik can help your operation, contact us today.

What Is Supervisory Control?
Supervisory Control, a critical component of SCADA (Supervisory Control and Data Acquisition) systems, serves as the overarching control mechanism for monitoring and managing industrial processes. In the context of SCADA, supervisory control systems allow operators to oversee multiple processes across different locations from a central point. This centralized control system collects data in real time from remote sites, processes it and provides operators with the necessary tools to manage and adjust operations efficiently.
These systems are integral in industries such as aerospace, automotive and medical manufacturing, where precise control over processes is essential.
Benefits of Supervisory Control Systems
By providing a comprehensive view of all operations, supervisory control systems enable more informed decision-making, improved process consistency and enhanced safety. They also:
- Centralize Monitoring: Operators can oversee multiple processes from a single location, improving efficiency and response times.
- Provide Real-Time Data Acquisition: Continuous data collection and monitoring help in identifying and addressing issues promptly, reducing downtime.
- Improve Process Control: Allows for fine-tuned adjustments to processes, ensuring compliance with industry standards.
- Improve Safety: With better control over processes, the likelihood of errors that could lead to safety hazards is minimized.
- Increase Productivity: Automated controls and efficient monitoring reduce the need for manual interventions, leading to higher productivity and cost savings.
Supervisory Control Applications
Supervisory control systems are used across industries for a variety of applications:
- Heat Treatment: Supervisory control systems are used to monitor and control thermal processing to ensure compliance with standards like AMS2750.
- Manufacturing Process Control: Supervisory control systems oversee and regulate processes like assembly lines, robotic operations, and quality control in manufacturing plants.
- Power Generation & Distribution: Supervisory control systems monitor the generation, transmission and distribution of electricity, including helping with load balancing, grid management and outage response.
- Pipeline Monitoring: These systems can control the flow of oil and gas through pipelines, ensuring safe operation by monitoring pressure, flow rates, and potential leakages.
- Water Treatment & Sewage Treatment: These systems can monitor and control water purification and treatment processes.
- Transportation & Infrastructure: Monitor and control traffic lights, optimize traffic flow, manage train movements in rail networks, and more.
- Building Automation: Monitoring and control of HVAC systems and security systems.
- Pharmaceutical: Manage precise conditions required for batch processing and chemical formulation.
- Food & Beverage: Control automated processing lines, monitor refrigeration units to maintain product integrity, and more.
We build systems using the best devices in the industry from leading providers like Honeywell, Watlow and Yokogawa. Your operations will become more effective, consistent and efficient with these superior supervisory controls.
Recommended Software for Supervisory Control
Conrad Kacsik recommends and often installs the SpecView HMI software, which provides companies with powerful automation, oversight and control of their equipment for a variety of use cases and industries. It offers a few key benefits:
- Ease of operation: This software was designed with the user in mind. Its operator interface can be programmed with customizable screens that automate tasks, decrease training time and simplify monitoring and operation—which all greatly reduces operator error. It also offers extreme flexibility. Access can be limited with passwords if desired, and users can automatically select the parameters and processes that best suit their specific needs and roles.
- Remote access: Its interface allows the operator to remotely view and control process instruments. The SpecView HMI package provides users a remote seat license so other users can log in to a local computer to review charts, write programs or control systems—remotely. Users can also receive email or text alerts in the event of an emergency.
- Industry compliance: The software helps users comply with regulatory requirements, including AMS2750 and Nadcap.
- Integration: SpecView integrates with the supervisory controls of all major manufacturers.
- Customization: The software makes it easy for us to customize screens so they include additional information, such as customer names, part numbers, part quantities—and any additional information you want to include with the process data. This can all be accomplished with either a keyboard entry or barcoding. We can even program SpecView to create a visual representation of your process. Graphics of your furnaces can be designed to show valve locations, various states and process variables. And additional screen applications can be developed for process details, batch reports, recipe management, loop turning and departmental overviews.
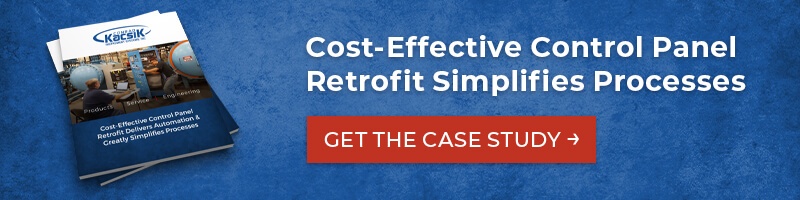